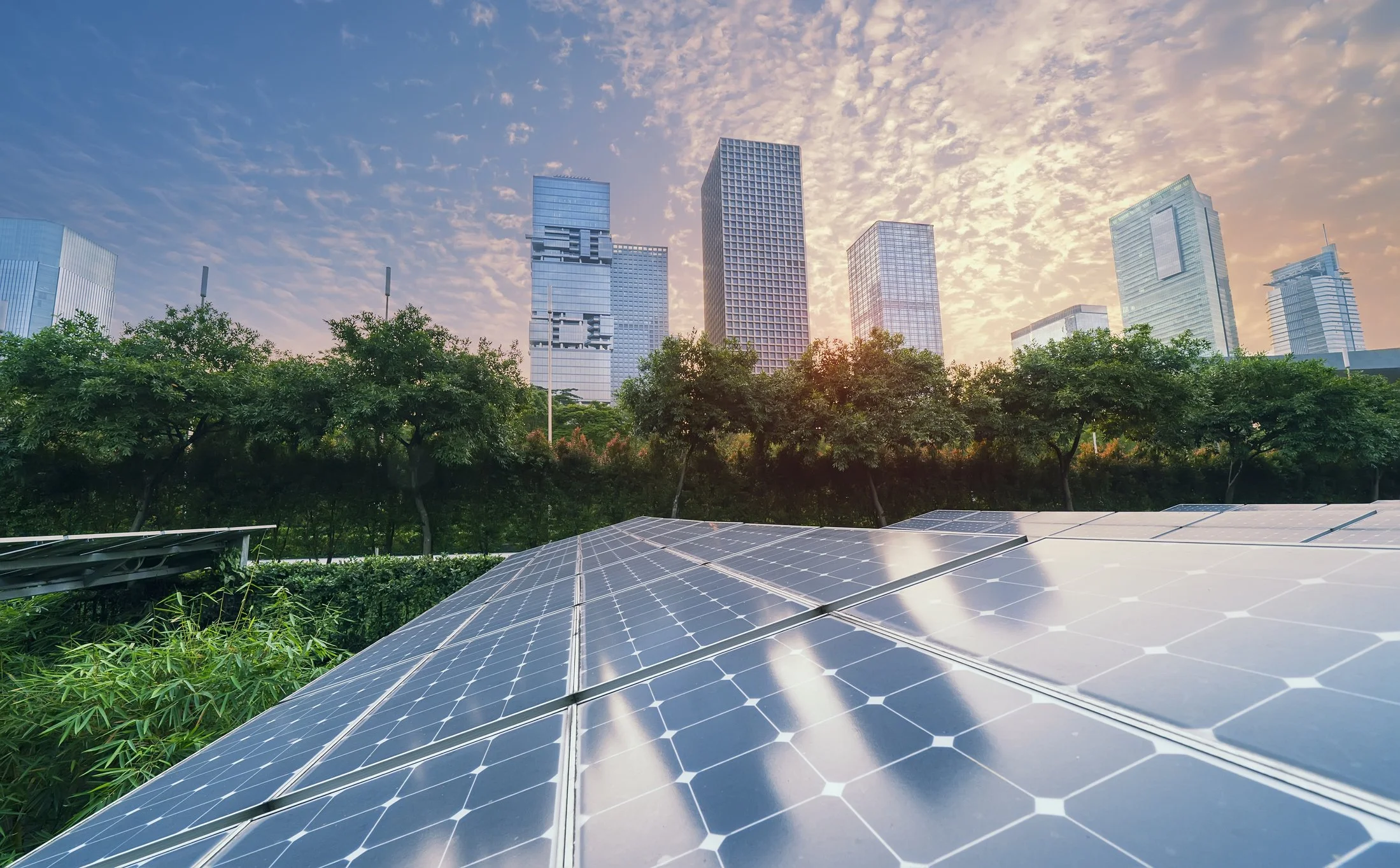
Theme 4: Smart Low Energy Production
Thermal Efficiency
Disruptive Processes: DRI and Near Net SHape Casting
This theme focusses on using smart techniques, enhanced material properties and non-carbon sourced reactants to reduce the net carbon usage and energy required throughout the steelmaking process.
Thermal energy lost as heat throughout the steel manufacturing process is considered together with both the use of new novel materials to convert conducted and radiated heat into useful electrical energy, as is the performance and durability of existing and future refractory materials.
Task 6: Thermal Efficiency
Project Leaders: Professor Cameron Pleydell-Pearce, Dr Hollie Cockings, Professor Matthew Carnie
Researchers: Dr Matthew Burton, Nicola Thomas, Dr Michael Dowd, Nigel Kougampillil, Ajitesh Sharma
Project Partners: Swansea University, British Steel, Celsa Steel UK, Liberty Steel, Sheffield Forgemasters, Tata Steel UK, Vesuvius PLC
Introduction
According to the International Energy Agency (IEA), heating accounts for 66% of industrial energy demand, which itself makes up 20% of total energy demand. Steel production represents a significant proportion of that demand and as there are some fundamental thermodynamic limitations to consider, such as iron’s melting point (1538oC) and its key solid state phase transformation temperatures (e.g. g > a at 920oC). Currently, a typical UK integrated plant loses 20PJ/yr through the largest heat vector. Task 6 of SUSTAIN looks to minimise loss through improved insulation, more efficient heat transfer and two key thermal energy harvesting technologies.
Aims & impact
The project aims to reduce waste heat production through insulation, process control and efficiency and thermal energy harvesting
Heating & Insulation
Develop a multiscale ex-situ structural characterisation approach for refractories
Improve understanding of structure-property relations in magnesia carbon refractories
Develop robust, cost-effective thermoelectric materials/devices for integration into refractory linings
Build a UK academic skills base in the field of refractories
Moveable Energy Storage as Heat (MESH)
Develop materials to harvest waste heat energy within selected temp ranges
Optimise heat capture and reutilisation with lab scale reactors
Model system energy flows from industry to determine heat capture efficiency, capacity and impact, both ecologically and economically.
Thermo-Electric Generators (TEGs)
Develop affordable printed earth abundant half Heusler TEGs
Ensure thermal stability and structural integrity in service
Progress to date
Heating & Insulation
So far we have developed and refined acquisition and segmentation approaches for X-Ray µ-CT data of carbon bonded refractory structures and completed oxidation experiments measuring de-carbonisation kinetics of graphite/phenolic based binder that occurs during pre-heating and between use cycles. Research has validated thermal stability and structural integrity characterisation method of carbon component using Raman spectroscopy and model free kinetics. These techniques are being used to assess industrially produced novel low conductivity refractory materials. Established unique TGA and furnace visualisation facilities that simulate demanding environments. This is related work in Task 12 (Feasibility Study project, Dr Yukun Hu) developed ML based furnace model to assess fuel switching capability and complimented by work in Task 14 (Feasibility Study project, Dr Yue Zhou) on using ML for scheduling andenergy management approaches to heating with renewable electricity.
X-ray µ-CT 3D volume analysis, investigating effects of mixing processes on fibre distribution in refractory materials a) standard; b) intensive.
Moveable Energy Storage as Heat (MESH)
The team have investigated charging behaviour of salt-in-matric (SIM) based thermochemical storage materials for heat storage under industrially relevant conditions. TEA has been completed on economic viability of the charging/ discharging of the material and associated logistics of transporting the heat to customers. Port Talbot steel energy flow review targeted temperature ranges of 50-200°C and 600-800°C. Each condition mapped low temp range allows continuation of Vermiculite CaCl2 SIM Materials, whilst higher temp range enables studies with the CaO/Ca(OH)2 system. Domestic hot water generation has been assessed via PhD.
Generating hot water from thermochemical materials. Water is contained within copper tubes, surrounded by our Salt in Matrix materials.
Thermoelectric Generators (TEGs)
N & P type Sn-Se thermoelectric materials have been produced and a novel screen-printing based method has been developed. Cementitious binders that improve high temperature properties with minimal efficiency penalties have been created and achieved improved efficiencies validating the manufacturing technique. ECR (Burton) has progressed to consider earth abundant P&N type Half Heusler economically scalable material options. Whole device testing is currently underway.
Summary of the demand / utilisation approach taken for Theme 4
Industry Context
The potential for impact of this activity is large. If say, 25% of that heat was recoverable the aforementioned ~ 20 PJ/yr were to be harvested, even at 5% efficiency, savings could be £10Million/year (based on an electricity price of £0.15/kWh). If the remainder was to be thermochemically stored it would provide enough heat for 500,000 homes that currently have a heating carbon footprint of 1.5MTCO2/yr. From a demand perspective, for just one process step alone, every 1oC saved through improved insulation would reduce costs by £400k/yr. Hence, there is commercial as well as environmental impetus for both reducing heat loss and recovering industrial waste heat.
Each sub-task has its own pathway to impact. Close cooperation between SUSTAIN, steelmakers and their refractory supply chain is being levered to characterize and pilot novel low conductivity materials at industrial scale (1-2 years per prototype). Data from the improved heat transfer efficiency studies will be fed straight into industrial process control models to realise immediate impact (3-4 years). Thermoelectric materials developed at lab-scale will first be implemented as self-powered sensor applications (3 years) in advance of large-scale harvesting at higher complexity (5-7 years). Finally, thermochemical charging demonstrators have already been commissioned in large buildings in partnership with the SPECIFIC® programme permitting rapid trialing of new materials at scale (2-3 years).