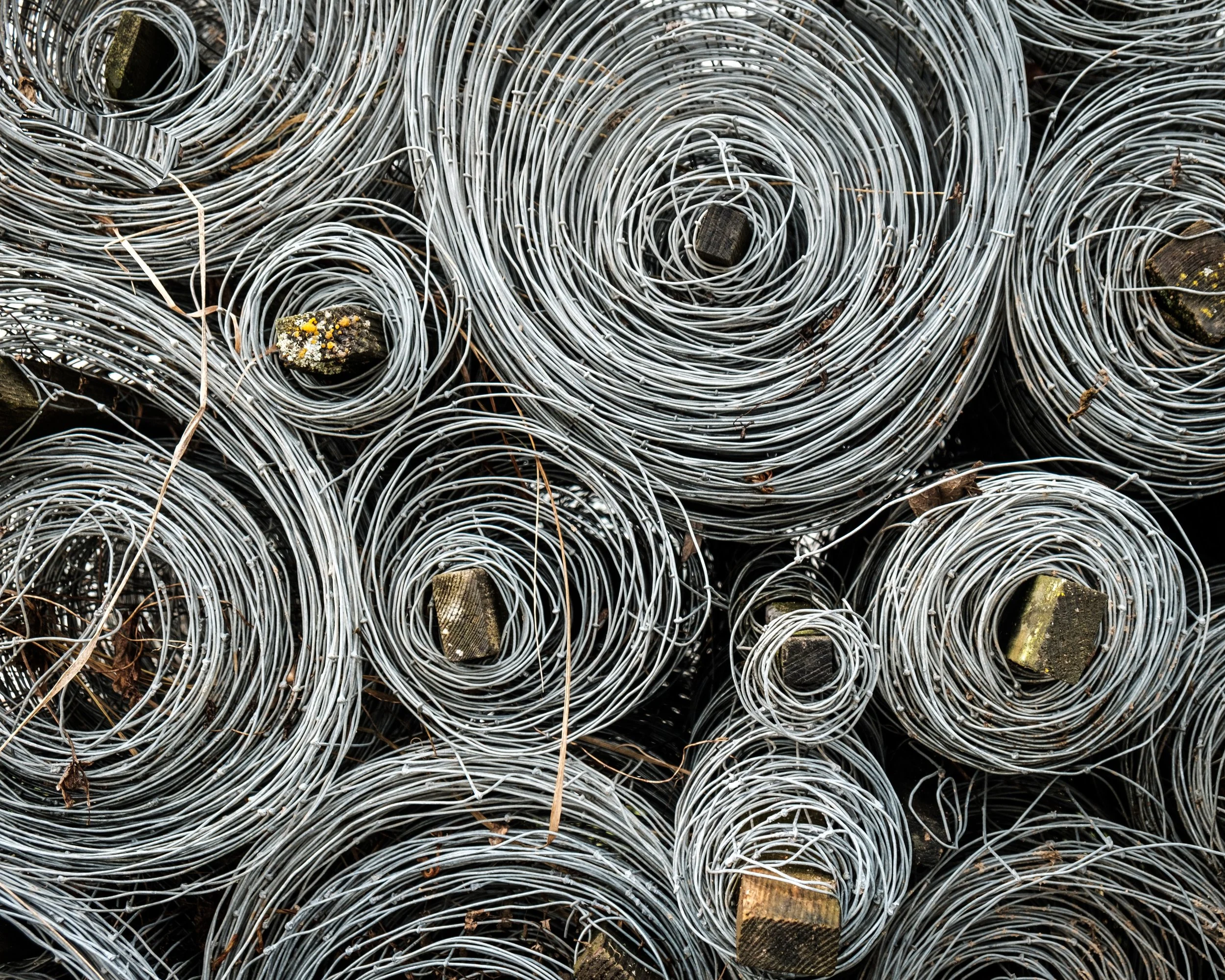
Theme 2: Zero Waste Steelmaking
Integrated Steelmaking to Reprocess Waste
Scrap Segregation and Utilisation
This theme concentrates on the reuse of domestic and industrial waste products within the steelmaking process. The projects here focus on the substitution of fossil fuels with applicable landfill waste and the reuse of end of life ferrous materials.
The UK currently exports approximately 10 M tonnes of scrap steel per year which could be recycled locally. The main challenge in its reuse is the management of unknown elements inherited from a range of steel types, and well as non-ferrous and non-metallic contamination, introducing impurities.
Task 2: Waste Reprocessing
Project Leaders: Professor Peter Holliman, Dr Richard Thackray
Researchers: Dr Eurig Wyn Jones, Fawas Ojobowale
Project Partners: Swansea University, University of Sheffield, Tata Steel UK, N&P Recycling
Introduction
Blast furnace ironmaking uses fossil fuel carbon (e.g. coke and coal) to provide energy and to reduce iron oxide to liquid iron. In this task, life cycle analysis will be combined with experimental testing to investigate using non-fossil fuel carbonaceous waste to displace fossil fuel carbon within the ironmaking process. By using non-fossil fuel sources of carbon we aim to reduce net carbon dioxide emissions and so help to decarbonise the overall process.
Planned impact
To displace fossil fuel carbon from ironmaking to reduce CO₂ emissions
Progress to date
We have used ultra-fast 20,000ºC/s pyrolysis to study the volatiles released from different non-fossil fuel carbon sources. These data have been baselined against currently used coals and correlated with chemical analysis and calorific values.
We have commissioned a new bomb calorimeter (purchased from a successful Welsh Government capital grant) and used this to measure calorific values (CVs) of different carbon feedstocks (fossil fuel versus non-fossil fuel). We have set up torrefication and hydrothermal carbonisation experiments to upgrade carbon feedstocks, to re-measure their CVs etc. and to compare this with the
processing energy to measure energy balance.
We have collaborated with Cardiff University to study rapid heat treatments (using their drop tube furnace) in combination with our ultra-fast pyrolysis to understand changes happening to carbon feedstocks over very short (i.e., 0-300 ms) timescales.
We have been developing ultra-fast thermal imaging and have applied this to different ironmaking scenarios (e.g., the sinter plant) to produce some interesting operandostyle data. We have thermally imaged samples within the visualisation furnace showing interesting thermal lag data. Additionally, we are commissioning a new thermal processing reactor to explore thermal transfer using a new ultra-fast thermal camera which we have purchased following a successful bid to the recent IMPACT capital fund.
The Sheffield EngD project (Lisa Ahmad) looking at life cycle analysis of alternative ironmaking materials started in Oct 2021. Zachary Lowther started a PhD at Swansea in Oct 2021 looking at fireproof insulation using waste slags and Sam Reis started an iCASE PhD at Swansea in Oct 2021 looking at environmental sustainability of ferrous sintering for the blast furnace.
Rationale for carbon substitution from Task 2
Pathways to industrial impact
We have been working with British Steel to look at biomass-derived coke and plastic waste as alternative carbon feedstocks for blast furnace. British Steel have already carried out some small-scale trials of different materials in their blast furnaces. A key part of the SUSTAIN research is to understand how different carbon sources behave in the blast furnace, and also to understand how changing raw material composition can effect operational conditions. Another issue is how blending
different carbon sources affects their behaviour. Ultimately, the pathway to impact will be driven by de-risking the technology change so that blast furnace operators can feel more comfortable with increasing the scale of fossil fuel displacement so that suppliers can then ramp up production and develop the supply chain.
Key findings
Thermal imaging provides useful insights in both slow motion and timelapse scenarios
Kinetics of thermal processes in blends is important to fuel switching
Ultra-fast pyrolysis GCMS can be used to study fuel switching by studying blends
Temperature lag varies considerably between materials which is important for energy transfer
Carbon feedstocks can be upgraded to improve their BF performance
Key Publication
Task 3: Scrap Utilisation
Project Leaders: Dr Zushu Li, Professor Claire Davis, Dr Richard Thackray
Researchers: Dr Mo Ji
Project Partners: WMG University of Warwick, University of Sheffield, British Steel, Celsa Steel UK, Liberty Steel, Sheffield Forgemasters, Tata Steel UK
Introduction
Increasing usage of steel scrap in either BF-BOF route or EAF route is an inevitable trend for steel industry because of its benefits in reducing CO2 emissions and energy consumption. However the residual elements present in the steel scrap could cause issues in steel processing such as hot shortness and segregation. In this task, the impact of residual elements on hot rolling process of free cutting steels and rail steels are evaluated. The outcomes of this research will provide a foundation for the optimisation of steel production processes and mitigate the negative impact of residual elements on steel processing and final steel quality.
Aims & Impact
The objective of this study is to enhance the utilization of UK domestically generated steel scrap in steel production, which aligns with the strategic goals of the UK steel industry. The focus is to assess the impact of residual elements present in steel scrap on the processability and final characteristics of high-quality steel products, and to raise the tolerance levels of residual elements during processing and in the final steel products.
Industry Context
The UK has the unique resource of abundant domestic steel scrap supply. The combination of scrap-based steel manufacturing and renewable energy presents a real opportunity to produce high quality steel at low or zero carbon output. The biggest challenge for the increased use of scrap is the impurities inherited from the scrap that influence the steel processing and service properties of steel products, particularly for automotive, aerospace, energy and railway applications. The outcomes of this project will provide recommendations to the steel industry to increase the residual tolerance of impurities in steels while maximising the scrap usage and reducing CO2 emissions.
Progress to date
In the as-cast free cutting steel, Cu was seen segregated at the MnS inclusion/matrix interface, in its metallic form. The Cu concentration near inclusions increased with depth from steel surface.
Cracks were observed in hot bending samples with 0.8 wt.% Cu at 1100°C (no cracks were seen for samples containing 0- 0.4 wt.% Cu). TEM examinations revealed that both metallic Cu and (Cu, Fe)S were distributed along grain boundaries adjacent to the crack front. Both phases were liquid at 1100°C, which weaken the grain boundaries and decrease the bonding strength between MnS and matrix.
To benchmark the effects of residual elements on microstructural development and property changes of steels, industry through process samples of free cutting steel (high residual levels) and pearlitic rail steel (low residual levels) have been characterised. The evolution of inclusions, pearlite colony size, surface ferrite fraction, interlamellar spacing, and microstructural changes throughout the process have all been evaluated.
Engagement with industrial partners enabled the identification of the key obstacles in increasing steel scrap usage in terms of the steel processability and properties, i.e. hot shortness, hot ductility, and machinability for the free cutting steel, and phase transformation kinetics and hardenability for the pearlitic rail steel.
For the free cutting steel, the residual element Cu was found to co-exist with inclusions in steel and with FeS at austenite grain boundaries during reheating/oxidation. The latter may effect the hot shortness and mechanical properties of the steel, which will be investigated by hot bending tests. The behaviours of residual elements and inclusions were found to vary through the as-cast slab thickness,
caused by changes in cooling rate during solidification.
This may effect their behaviours during later processing (rolling, drawing) and therefore final properties. Further studies will be performed.
Measuring the pearlitic transformation kinetics (e.g. pearlite colony growth) using High Temperature Confocal Laser Scanning Microscopy (HT-CLSM) was preliminarily proved to be an effective approach. Tests at different cooling rates for steels with high and low residual elements will be carried out to examine the transformation kinetics and hence pearlite interlamellar spacing and resultant final strength.
Key findings
The cooling rate during solidification through the as-cast slab thickness affects the inclusion behaviours and residual elements distribution
Eight categories of inclusions have been identified in the as-cast samples of low carbon free cutting
steels with presence of Pb and CuCu co-exists with FeS at austenite grain boundaries during oxidation at 1100°C, which may effect hot shortness and steel mechanical properties
HT-CLSM was successfully trialled to in-situ measure the pearlite transformation rate